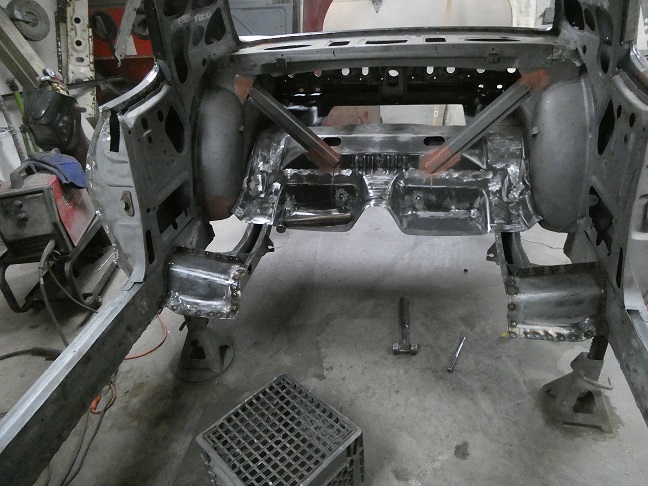 |
The rear torque box caps did not really need to come off this car, but in an attempt to get inside all of the nooks and crannies to eliminate all rust, I cut the caps off. The insides were sandblasted and epoxied primed. Welding the caps
in is not very difficult, but they had to be adjusted to get them to fit correctly.
|
|
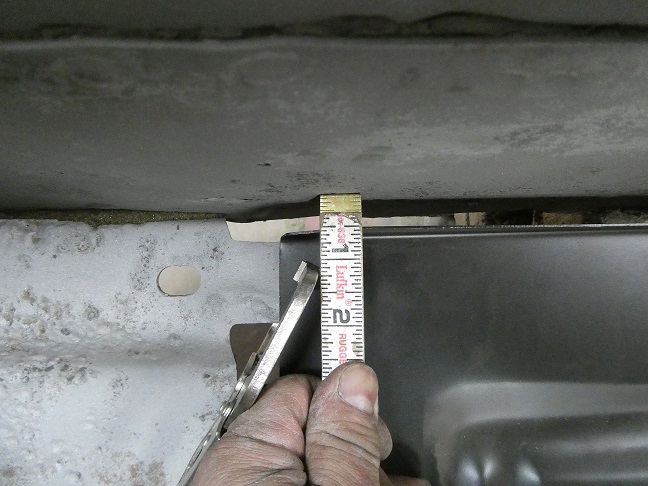 |
Dropping the floorpan in place quickly revealed that it was not wide enough. It is known that the rear corners are different between Mustang and Cougar as Cougars have longer wheelbases. I think it has been assumed that otherwise the floorpans are the
same, but they aren't. I believe that Cougars are wider. On this car a gap of 5/8" was evident on one side when the other side was clamped in place. I did a bunch of research on the web, but have found very little content on the subject. I think it is either
no one wants to admit to their repair or just don't want to say in an open forum that the parts don't fit. THEY DON"T FIT ON COUGARS!
|
|
|
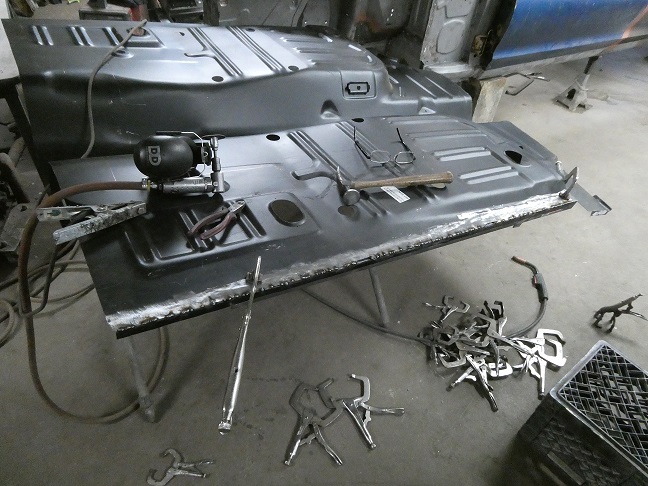 |
In my reserch I have seen where some people have welded angle iron along the rockers to fill the gaps. I've also read that some people jump up and down on the hump to spread it wider. Some people use comealongs to pull the rockers closer together, which is basically changing the
width of the car..... Me, I chose to actually correct the floorpan.
I bent one of the flanges flat to get the width right. Then I welded a strip of metal across the length of it to form a new flange.
To keep the floorpan flat I clamped a long piece of angle iron across the new flange and butted the new strip of metal along the angle iron. After tackwelding in the new flange piece, I removed the angle iron.
|
|
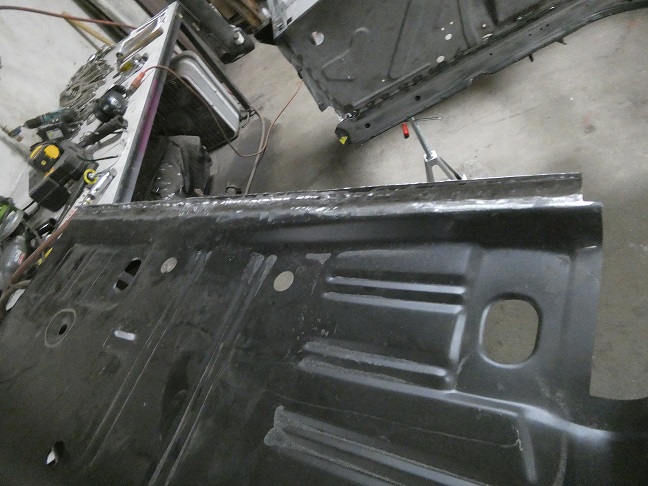 |
And here you have it, a properly widened floorpan.
|
|
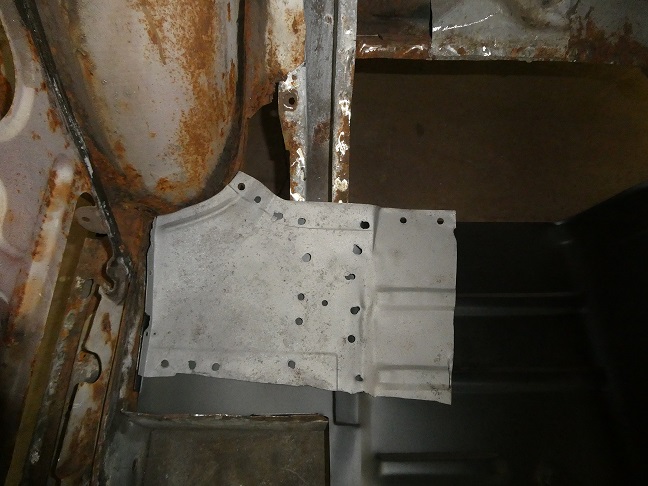 |
Moving on the the rear corners. As you can see in the picture on the left, there is a large gap between the floorpan corner and the inner wheelhouse. In the other picture you can see a section of a floor from a Cougar. After lining it
up, I screwed the piece down for welding later.
|
|
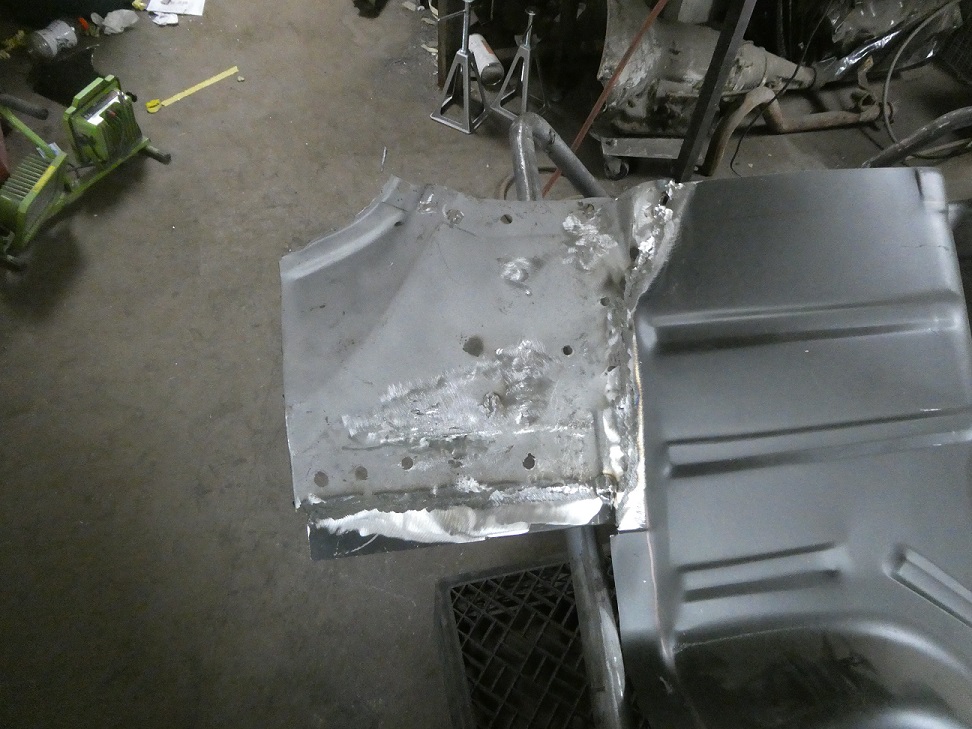 |
With the floorpan removed the new rear quarter section was grafted in place.
|
|
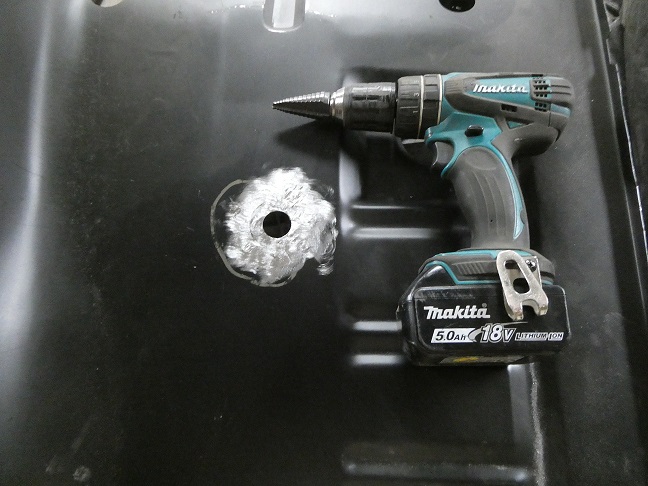 |
Just like the trunk drop off panels, there were incorrectly stamped dolly holes. "dolly holes" are the holes that pins went through at the factory that held the body going down the assembly line. These needed to be fixed, first because the recess
actaully interfered with the front frame rails and second, I wanted them to be correct if the they arenlt seen.
The repair is quite simple, cut some slits, hammer it flat, weld up the slits, smooth out the welds and then drill out the center to the correct diameter.
|
|
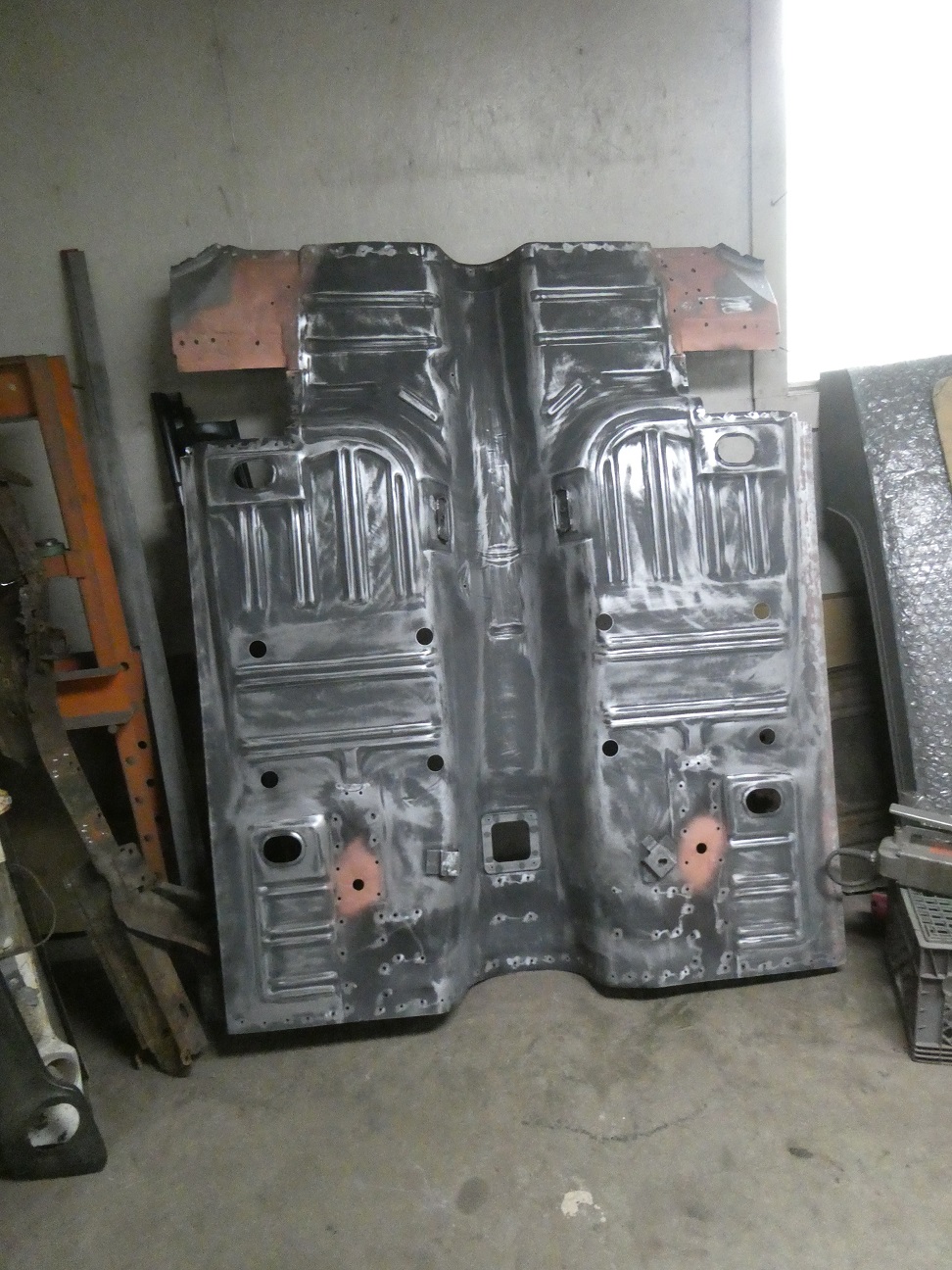 |
The bracket for the shifter is not quit the same as the original. The originals are a bit larger and the nuts are rectangular versas round. I neded up getting a really nice one off a car, cleaned it up and welded it to the new floor pan.
Once the parking brake brackets were welded in, the floor pan was sanded and then a ton of holes were drilled into it for plugwelding it to the body. Sorry no pictures of it going in.
|
|
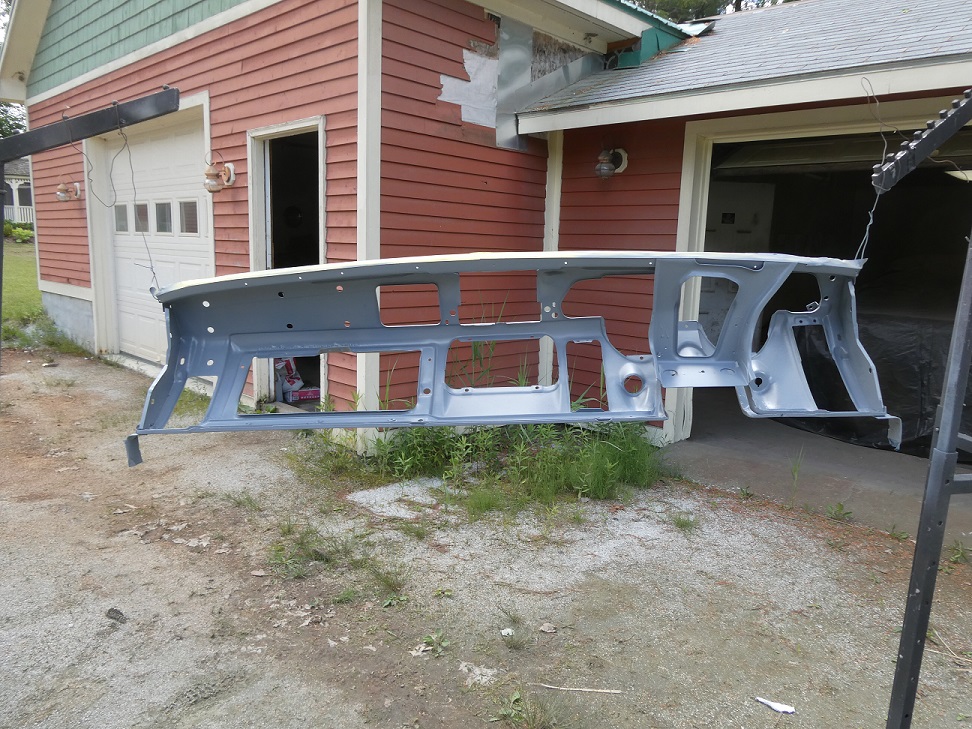 |
Next up was the dash. The dash only needed a small repair before it was put in epoxy primer.
|
|
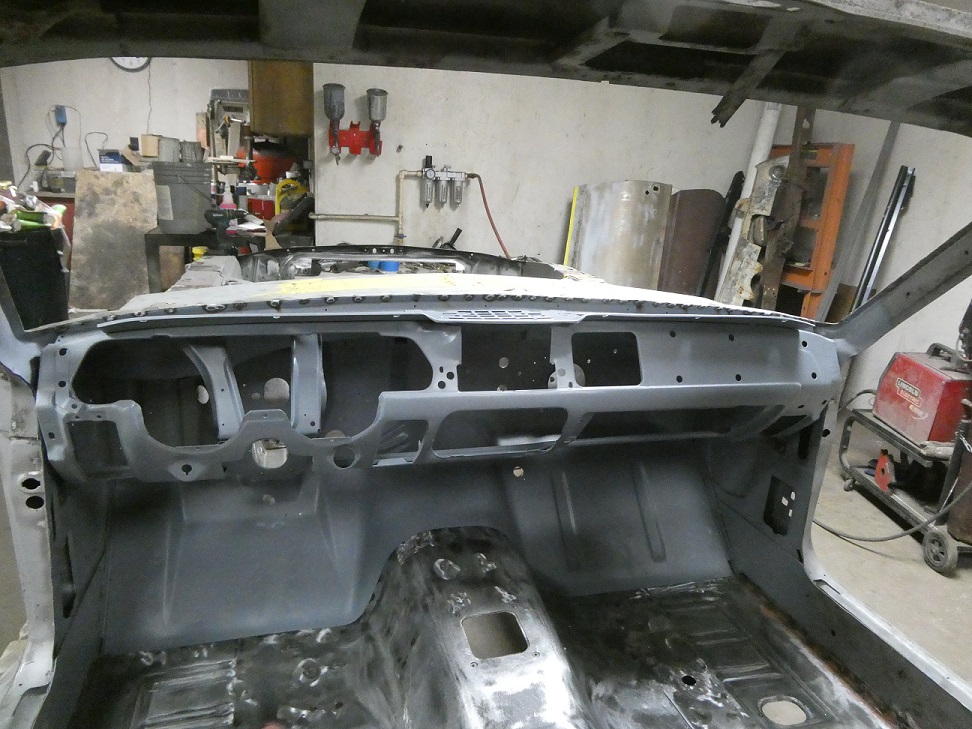 |
The dashs to these cars were welded in place up to 1968. The top is welded all along the upper cowl and the bottom is spotwelded to the lower A-pillars. Before welding in the dash the inner firewall had to be prepped and primed.
|
|
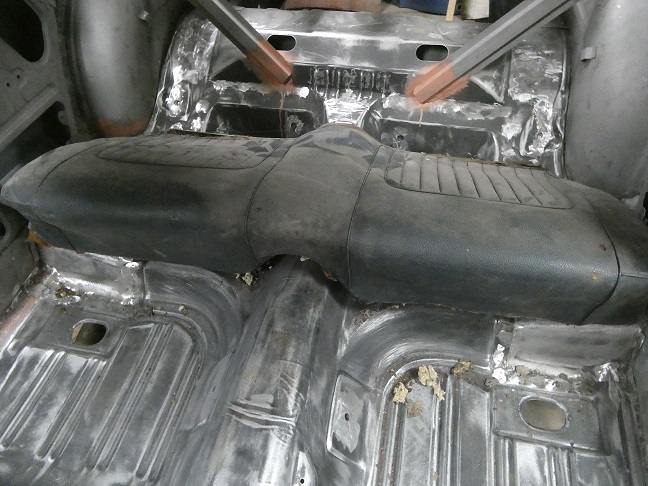 |
And final the last piece of metal to be welded on the inside of the car were the rear seat lower brackets. It is recommended to use the actual seat to locate the brackets before welding them in.
|
|