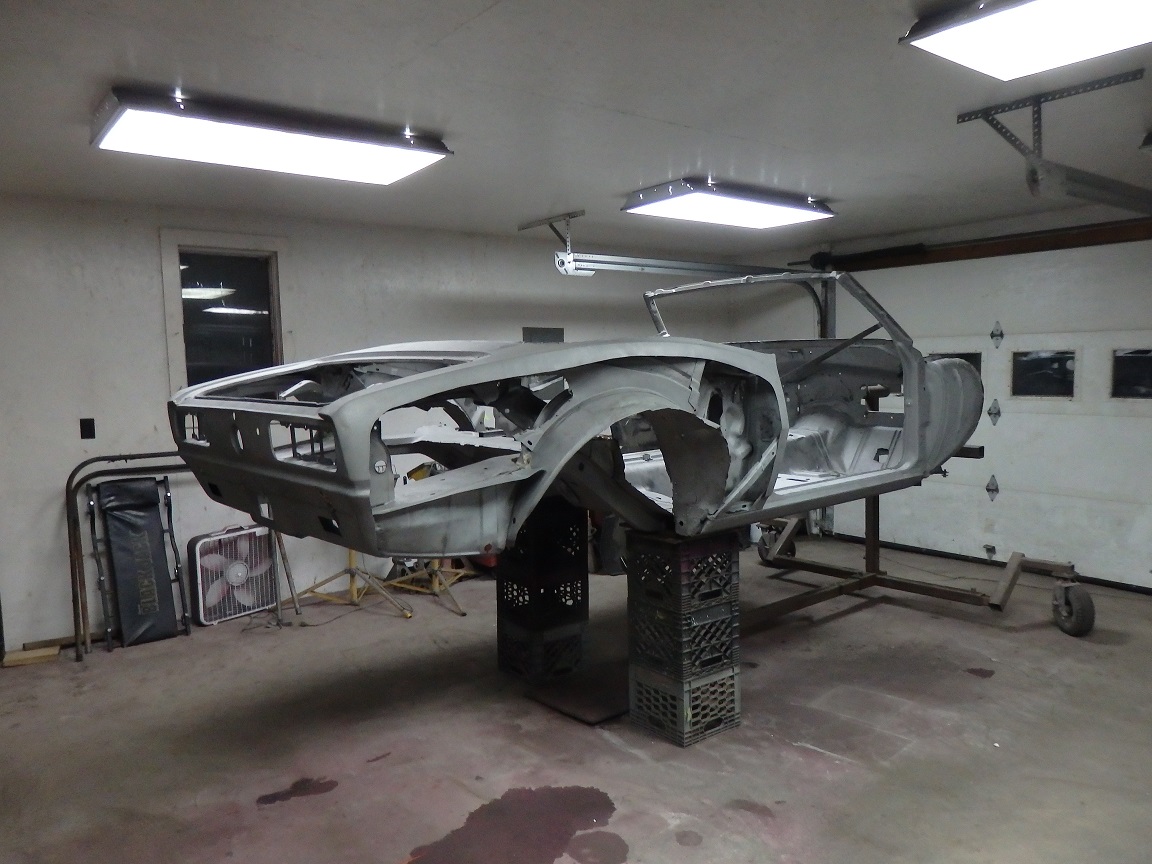
Here it is ready for the first batch of metal work. First up, the entire rear end of the shell, which is pretty much most of the work.
|
|
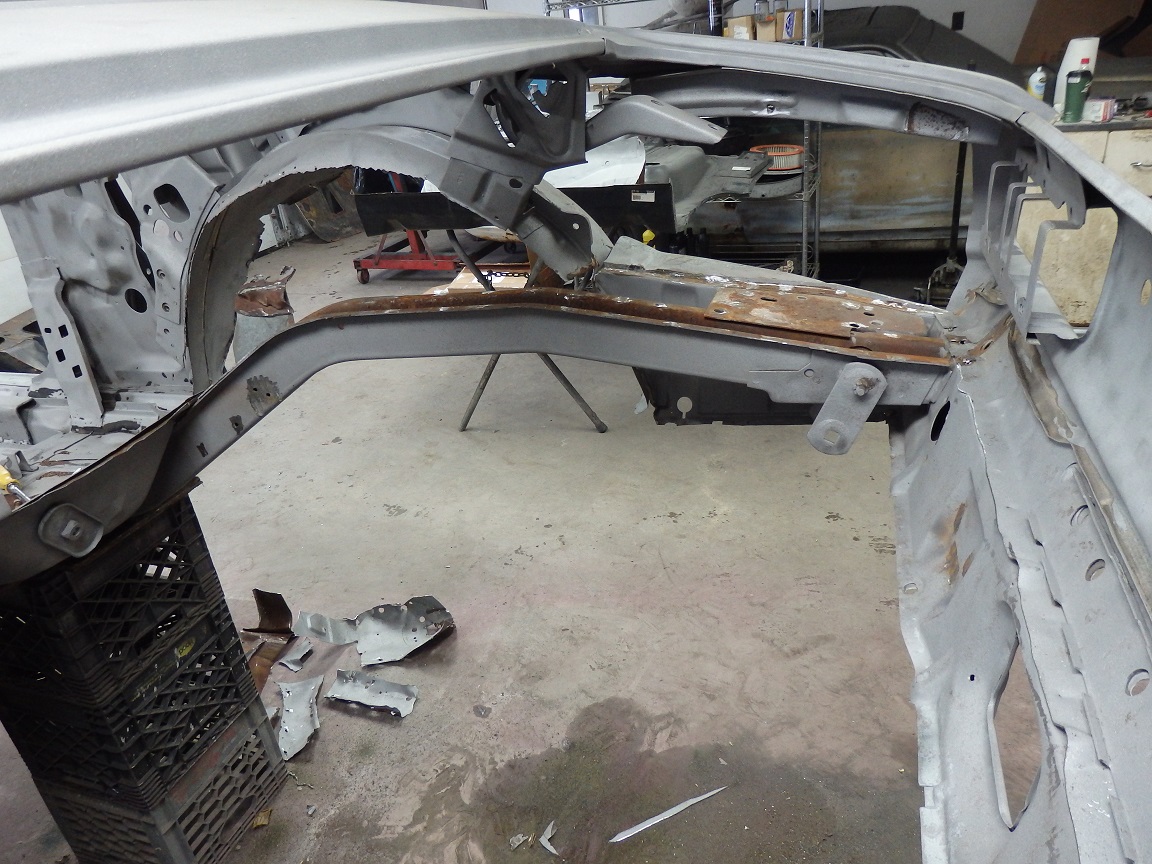
There was so much damage to the trunk pan that the whole thing had to be replaced. To maintain as much of the original factory look as possible, I left the rear of the trunk
pan and the supports for the shakers in place. In the above pictures, I had not touched the inner wheel houses. That's the way I got the car !
|
|
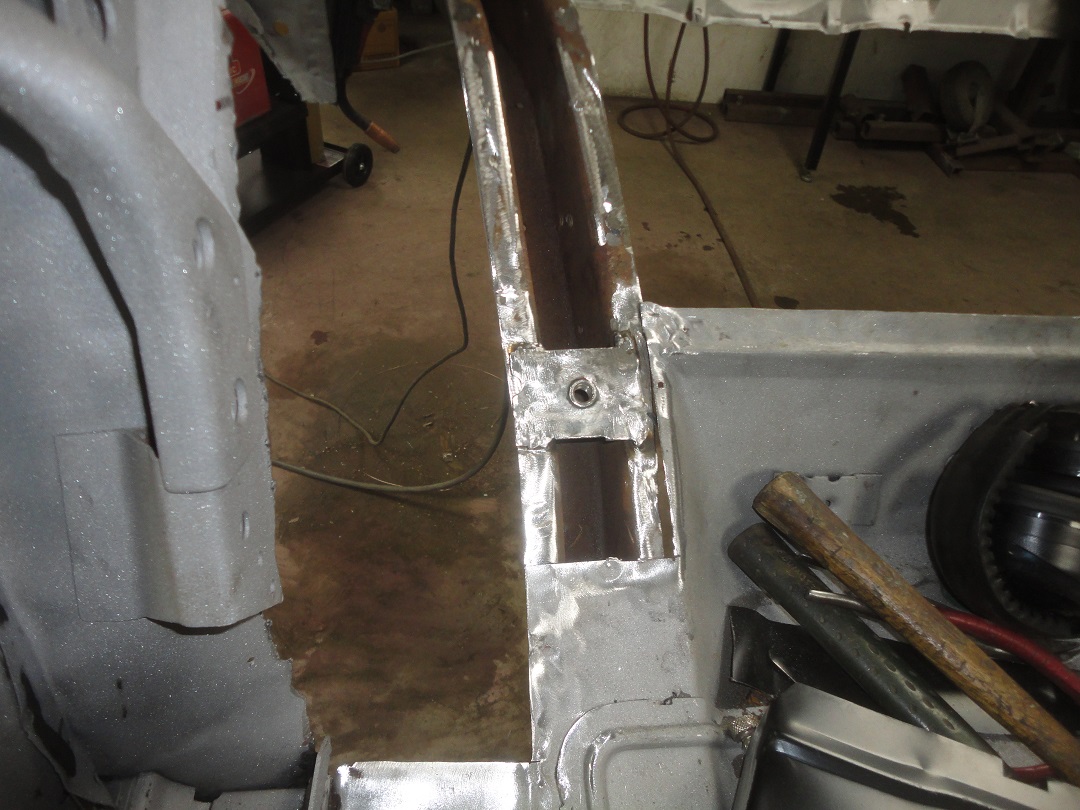
The car had a roll cage welded in it, with only the anchor plates remaining when I got the car. The plates were welded over the rear seat belt mounts. Since the rear floor
was cut away to tub the car, it was easier to just cut that area out and weld the seat belt mounts to the frame. Then I butt-welded in a new floor section.
|
|
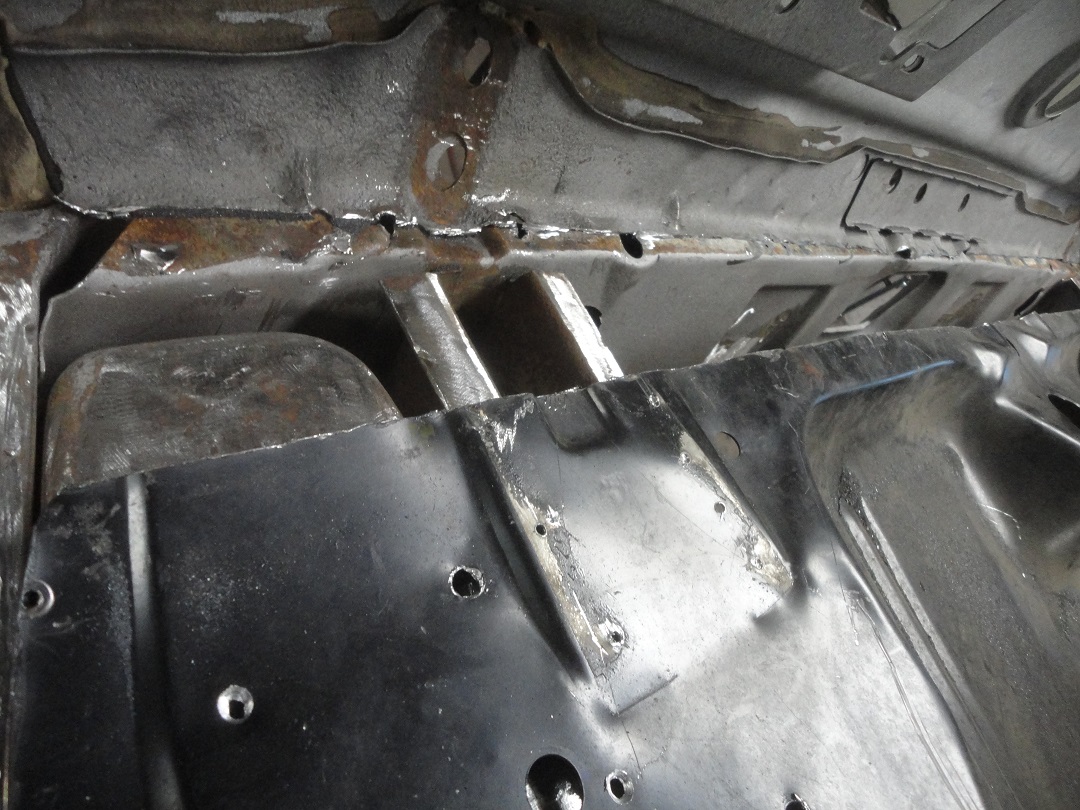
The new full trunk pan was trimmed and fitted in place. If it wasn't for the fact that the wheel houses where chopped up, it would have been impossibly to fit it without
removing the tail panel. With the pan fitted in place, a tape reference line was used as a guide. With the new pan resting on top of the edge of the old pan, a disk cutter was used
to cut through both pieces simultaniously to ensure a perfect fit for butt-welding.
|
|
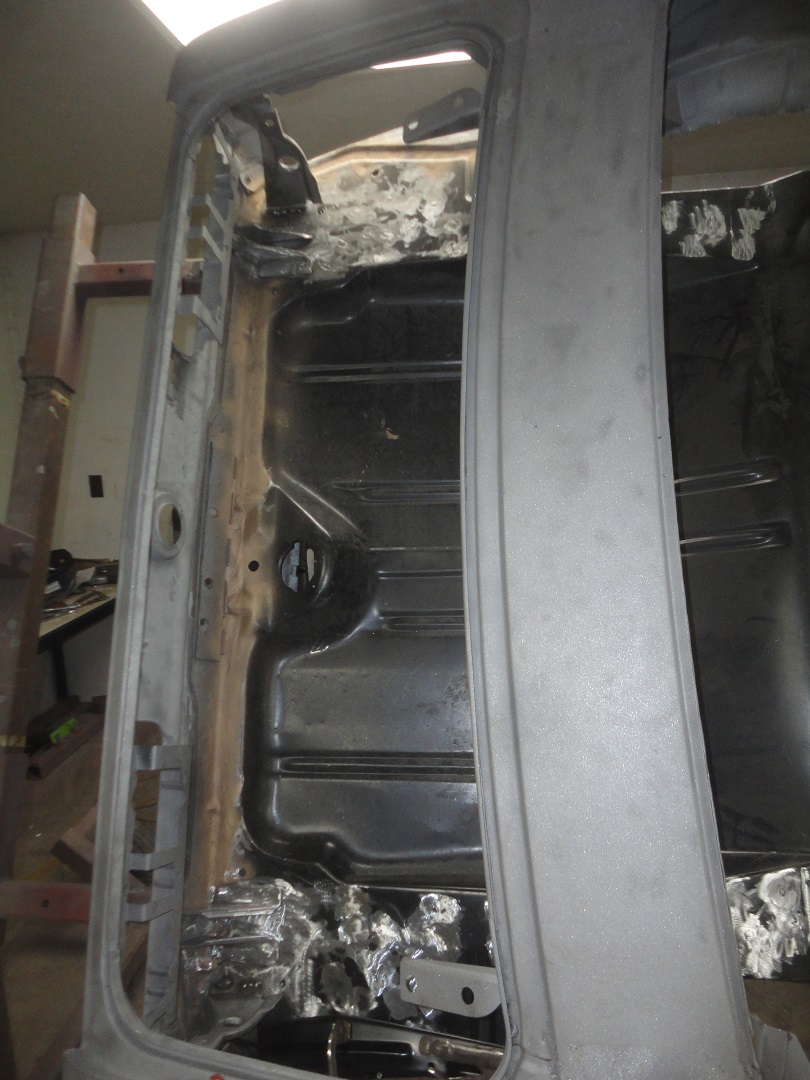
With the trunk pan welded in place, the shaker mounting brackets were welded back in using the shakers to set them in the correct position. The original bumper support braces
were also welded back in. The braces that were welded to the repo trunk pan did not look as correct. The trunk latch support was left off until after the inside of the tail panel could
be primed.
|
|
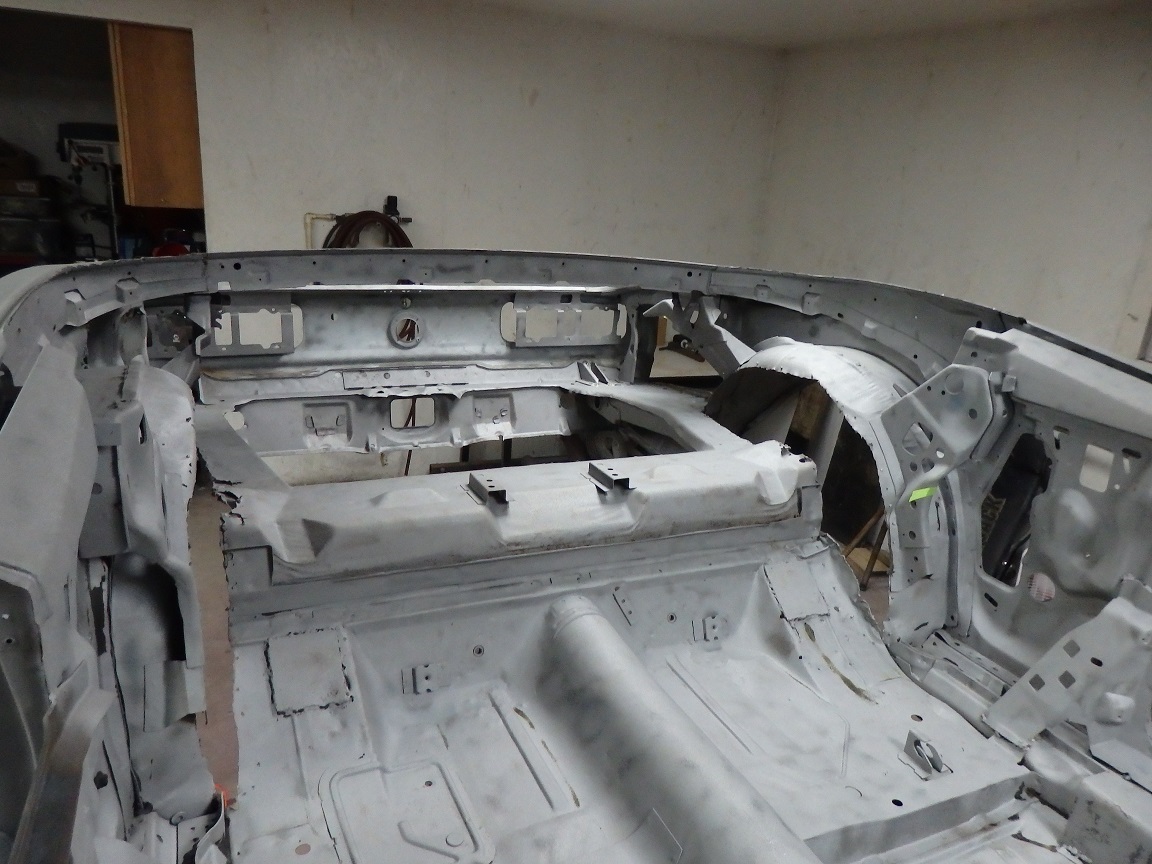
Here's a comparison between the new floor and what it looked like when I started. The convertible pump mount brackets and upper shock mounting plates still needed to be
welded in at this point.
|
|
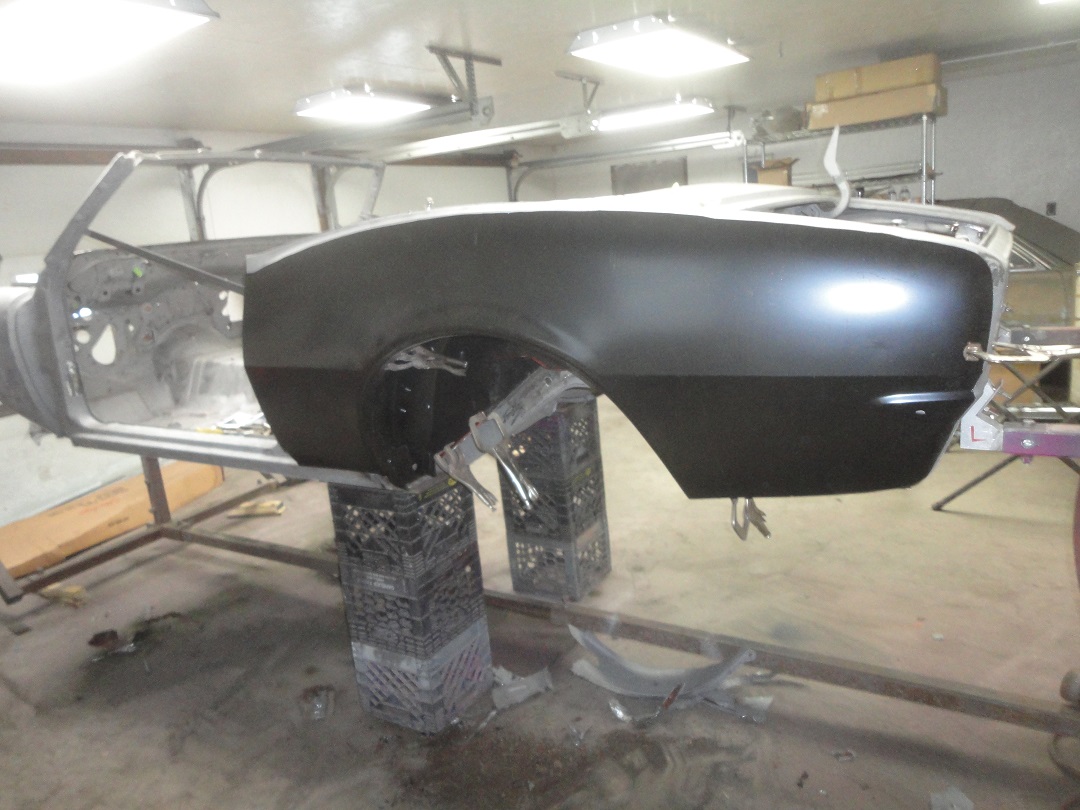
Next came the driver's side wheel house. The inners are different in 67 then later years and they do not make correct outers for 67 convertibles. I had to modify the repos that were for coupes. The wheel house
pieces were screwed together and were then screwed in place. Once happy with their alignment, I took them out and welded the halves together. I took the primer off with an orbital sander and then screwed them back in.
A square was used to confirm that they were still fitting correctly. The quarter was also used to confirm fit and to properly clamp the trunk lower drop-offs in place.
Welding the wheel house in did not take very long. Just lots of plug welding and some grinding to dress the welds. Part of the trunk hinge support had been cut off when the car was tubbed, so I had to make a piece
to weld in to make it look correct again.
|
|
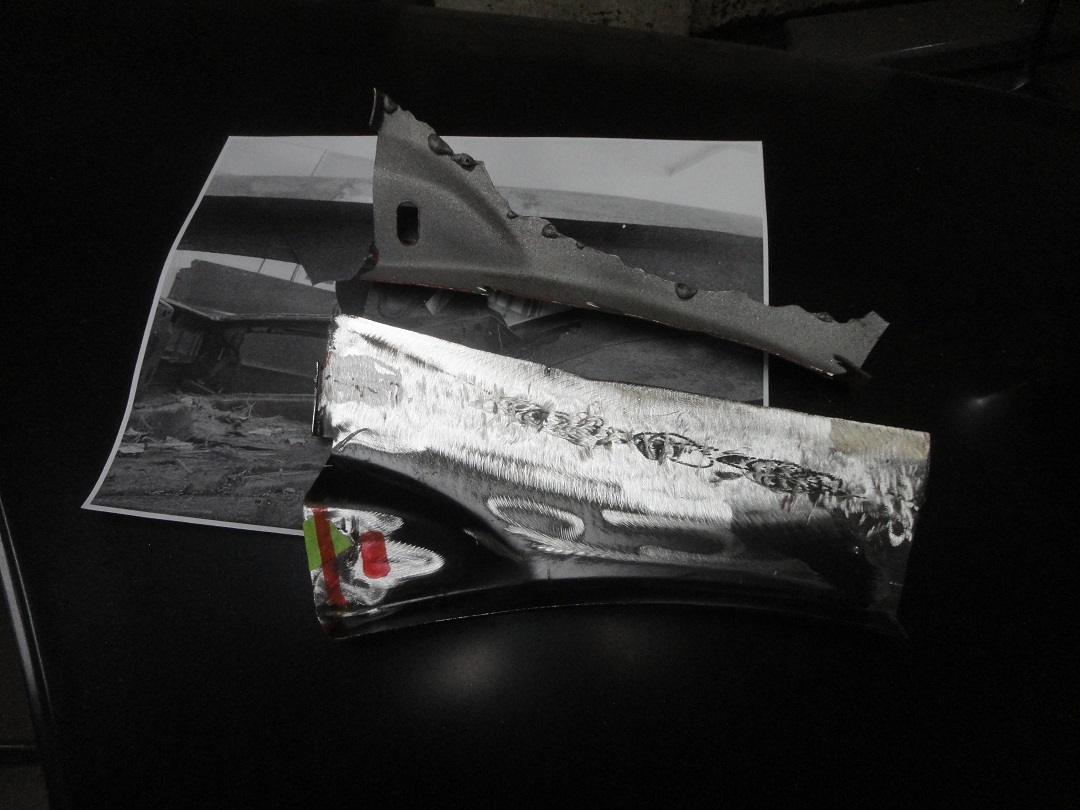
As part of converting the car to a drag car, someone torched a big section out of the right rear reinforcement. Repos are available, but they are single piece, while the original is made from several pieces.
I cut the top section down to what I needed. The bottom section I had to weld extra metal on to replicate the original piece. And of course, I had to trim it back and move the alignment hole since the repo
part wasn't correct.
|
|
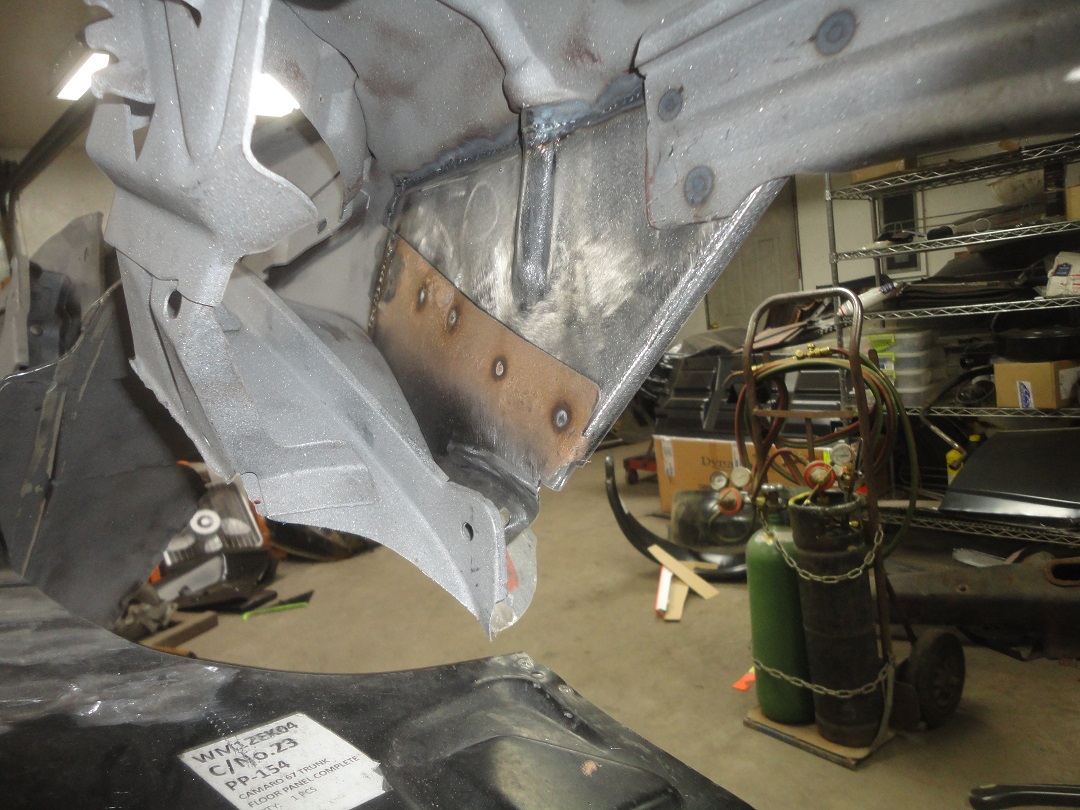
The top piece I just butt-welded in place and trimmed the bottom to follow the line of the original piece. I followed a similar process for the bottom section. The last picture showed the view
from the inside before I detailed the welds and drilled the aligment hole in the upper piece to match the other side. I think it came out great.
|
|
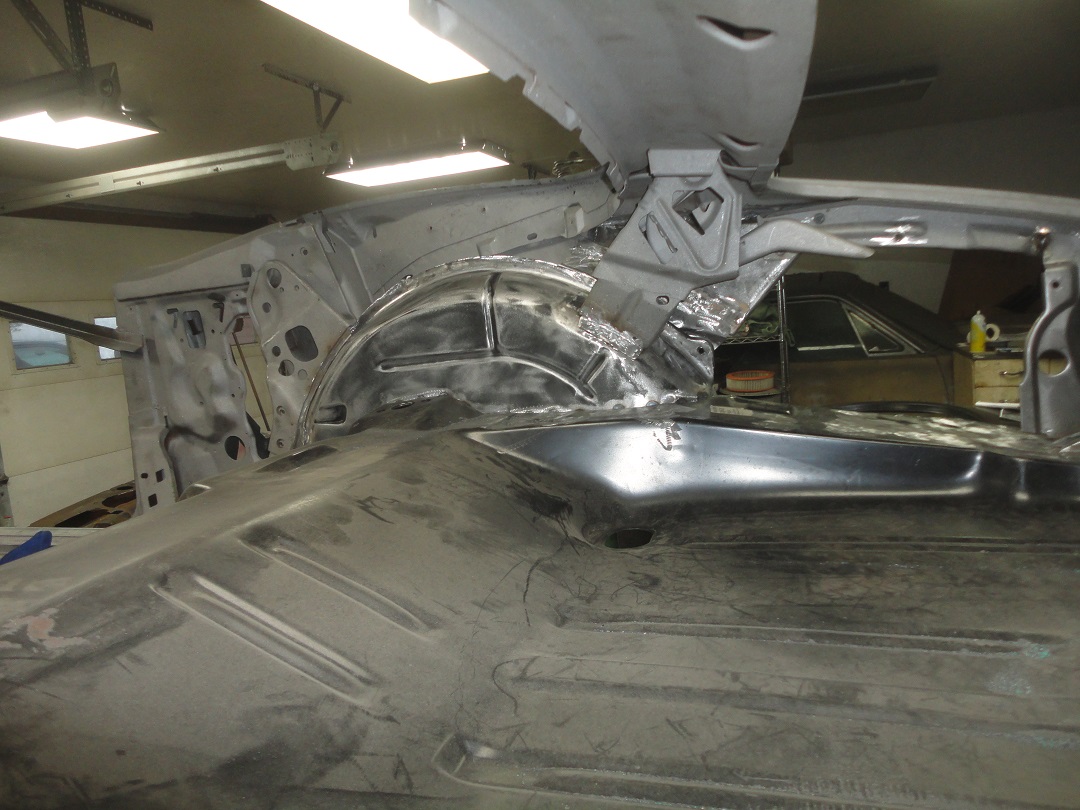
Next came the replacement of the RH wheel house. The process started with bracing the car to keep the frame in alignment. Once braced the alignment was measured and compared to the factory frame alignment
specs from the service manual to ensure that the alignment was correct.
As with the other side, the wheel house halves were welded together and were screwed in place prior to welding them in. As with the other side I had to make a piece to replace the section that was cut off the trunk hinge bracket.
|
|
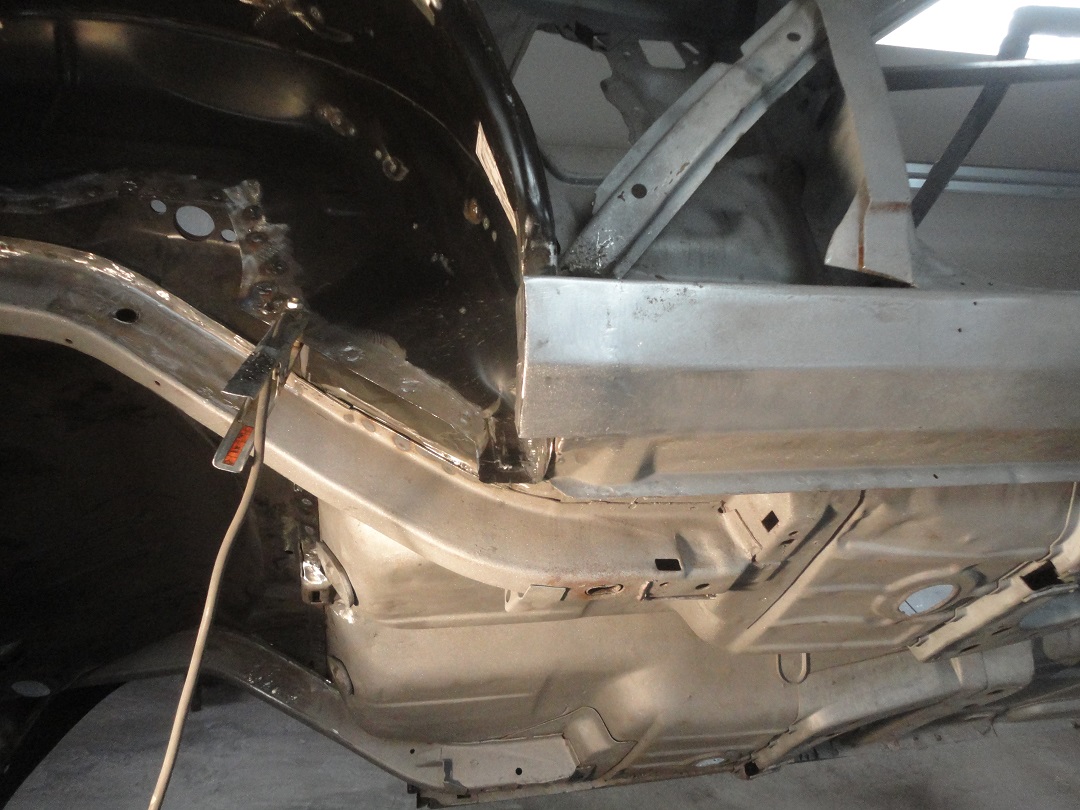
As part of converting (butchering) the car to a drag car, someone had cut the ends of the rocker panels off and hammered the outer wheel houses flat at the rockers.
I had to buy a pair of outer rocker panels just to get the last couple inches off from them. Using repo quarters and confirming with my 1969 FIrebird
Convertible I was able to confirm that the rocker panels end 13.0 inches from the edge of the B-pillar. I trimmed the rockers back to a nice undamaged area
and cut the ends off the repo rockers to butt-weld in place. Word to the wise: Mig-Welders do not like magnets...
|
|